Humanoid Robots Are Transforming Manufacturing: A World-First Deployment
In a groundbreaking move for industrial automation, Shenzhen-based UBTECH Robotics has successfully deployed a fleet of humanoid robots at Zeekr’s 5G smart factory in Ningbo, China. This marks the world’s first large-scale, multi-task collaboration between humanoid robots in a live manufacturing environment. These advanced robots are not only working alongside humans but also coordinating among themselves to streamline production.
A New Era: Multi-Robot Coordination in Manufacturing
Traditionally, industrial robots have been limited to single-task automation, but UBTECH’s Walker S1 humanoid robots represent a leap forward. For the first time, dozens of robots are performing various functions across different zones within a real-world factory. These include:
- Collaborative Sorting: Using advanced vision systems, the robots can accurately sort and organize car components with a precision of 99.7%.
- Large Payload Transport: Robots can collectively carry and position heavy items, overcoming challenges like uneven load distribution and complex trajectories.
- Precision Assembly: With force-torque sensors, the robots handle delicate tasks, such as installing car doors with millimeter-level accuracy.
The Brain Behind the Robots: UBTECH’s BrainNet AI System
At the heart of this revolution is BrainNet, UBTECH’s proprietary AI system. It enables robots to function in a synchronized manner by dividing cognitive processing into two levels:
- Super Brain (Cloud-Based AI): Responsible for high-level planning, task scheduling, and decision-making.
- Smart Cerebellum (Onboard AI): Controls real-time motion, adapts to the environment, and ensures safety during operations.
This system processes over 1.2 terabytes of sensor data per hour, allowing the robots to dynamically redistribute tasks, optimize workflows, and even monitor power usage for efficiency.
The Role of Advanced AI in Industrial Robotics
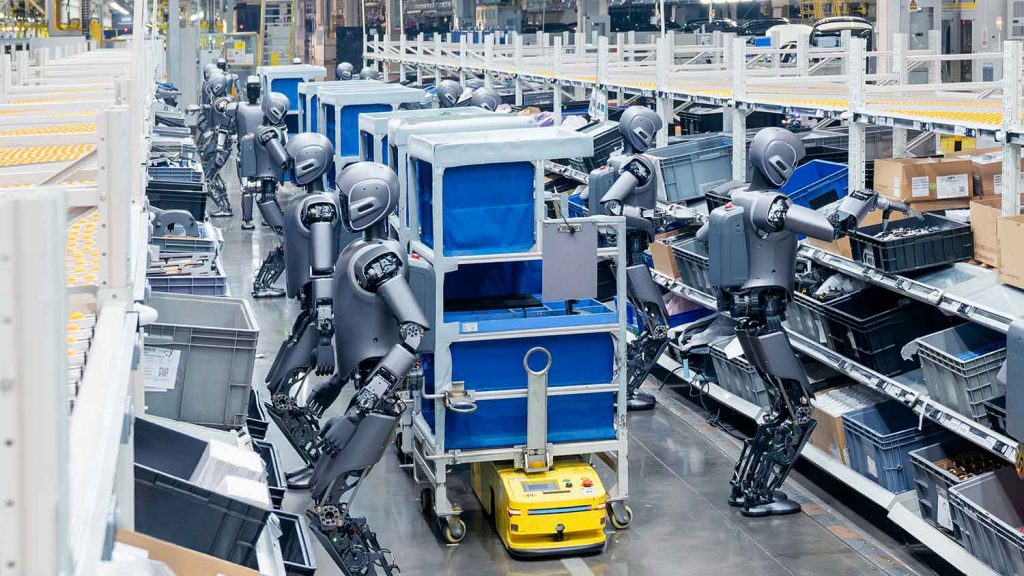
UBTECH’s humanoid robots are powered by the DeepSeek-R1 multimodal AI model, trained on over 100 million industrial datasets. This allows them to:
- Predict human movements to avoid collisions.
- Adapt to new tasks through reinforcement learning.
- Execute complex instructions by combining speech and gesture recognition.
With this level of intelligence, the robots reduce downtime, enhance production efficiency, and improve overall factory flexibility.
Industry Adoption: The Road to 5,000+ Humanoid Robots
UBTECH has established strategic partnerships with major automotive manufacturers, including:
- BYD: Developing robots for battery module handling.
- Geely (Zeekr’s parent company): Customizing software for electric vehicle production.
- Foxconn: Optimizing logistics automation across multiple warehouses.
Following successful trials, over 5,000 humanoid robots are expected to be deployed in Chinese factories by 2026.
The Future of Intelligent Manufacturing
This deployment marks a shift from semi-flexible manufacturing to fully flexible intelligent manufacturing. Key benefits include:
- 40% reduction in production changeover time.
- 25% decrease in material waste through real-time quality monitoring.
- Automated reconfiguration of production lines within hours instead of days.
With humanoid robots now proving their efficiency, manufacturers worldwide are taking note. Tesla’s Optimus team and BMW’s automation division have already expressed interest in UBTECH’s technology. As AI and robotics continue to evolve, factories of the future may operate with minimal human intervention, maximizing efficiency and precision.
The revolution is no longer coming—it’s already here.
Related article: Get Ready for Robots: The AI Intelligent Robot Science Exhibition Comes to Haikou!
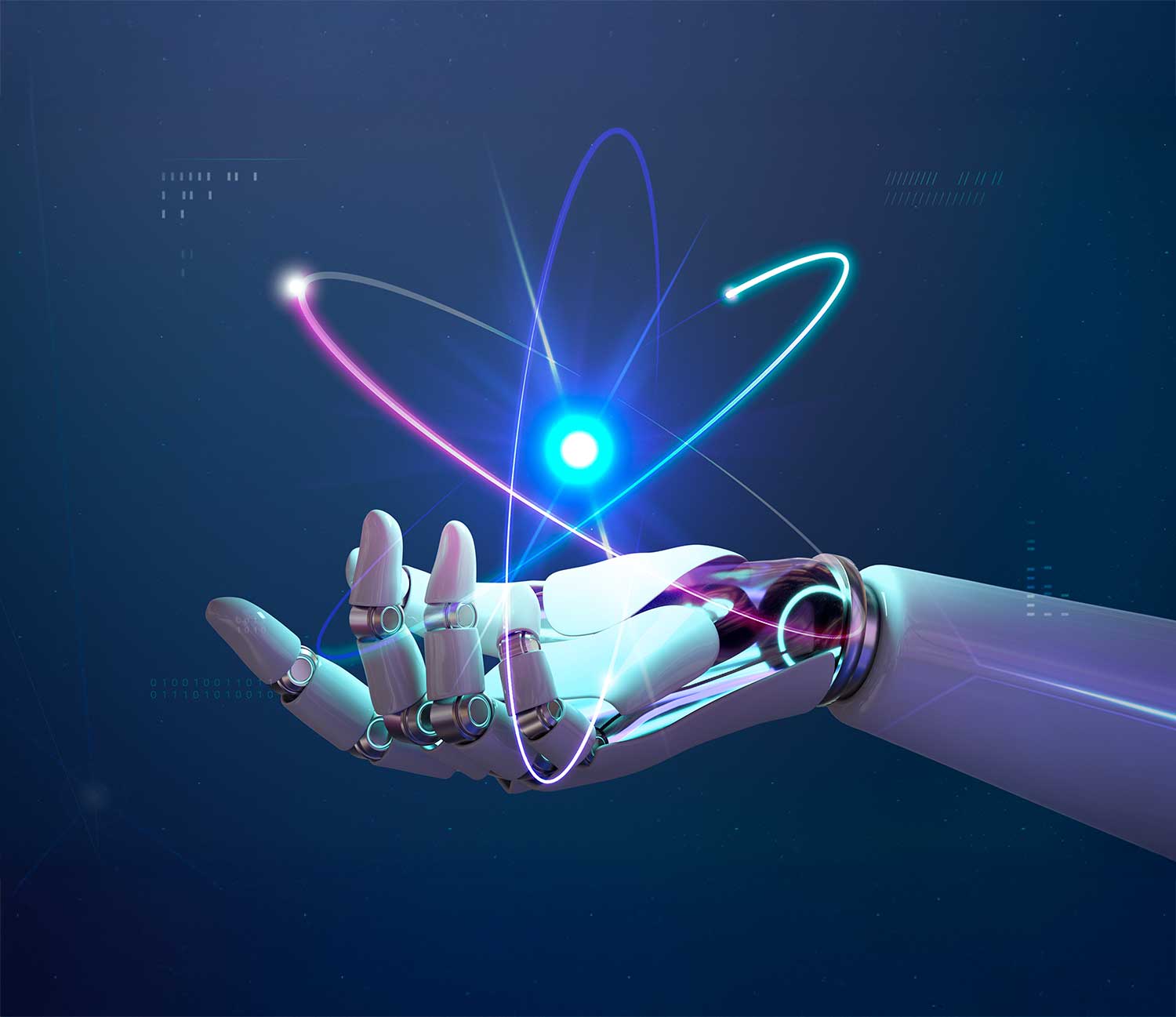